SMT использует традиционную паяльную пасту для анализа и решения сварочной полости с воздушным оплавлением (Essence Edition 2023), вы этого заслуживаете!
1 Введение

При сборке печатной платы паяльная паста сначала наносится на паяльную площадку печатной платы, а затем прикрепляются различные электронные компоненты. Наконец, после печи оплавления оловянные шарики в паяльной пасте плавятся, а все виды электронных компонентов и паяльная площадка печатной платы свариваются вместе для сборки электрических субмодулей. Технология поверхностного монтажа (sMT) все чаще используется в упаковочных продуктах с высокой плотностью размещения, таких как корпуса системного уровня (siP), устройства ballgridarray (BGA), а также силовые чипы, квадратные плоские корпуса без выводов (quad aatNo-lead, называемые QFN). ) устройство.
Из-за особенностей процесса и материалов сварки паяльной пастой после сварки оплавлением этих устройств с большой поверхностью пайки в зоне паяльной сварки появятся отверстия, что повлияет на электрические свойства, тепловые свойства и механические свойства продукта. даже привести к выходу продукта из строя, поэтому улучшение сварочной полости для оплавления паяльной пасты стало технологической и технической проблемой, которую необходимо решить, некоторые исследователи проанализировали и изучили причины сварочной полости шарика припоя BGA и предложили решения по улучшению, обычный припой сварочный процесс оплавлением пасты, зона сварки QFN более 10 мм2 или площадь сварки более 6 мм2. Решение для голой стружки отсутствует.
Используйте сварку Preformsolder и сварку в вакуумной печи с обратным холодильником, чтобы улучшить качество сварного отверстия. Сборный припой требует специального оборудования для точечного флюса. Например, чип смещается и сильно наклоняется после того, как чип установлен непосредственно на сборный припой. Если чип для монтажа флюса подвергается оплаванию, а затем точечному, процесс увеличивается на два оплавления, а стоимость сборного припоя и флюсового материала намного выше, чем стоимость паяльной пасты.
Вакуумное рециркуляционное оборудование более дорогое, вакуумная емкость независимой вакуумной камеры очень низкая, экономическая эффективность невысокая, а проблема разбрызгивания олова серьезная, что является важным фактором при применении высокоплотных и малых шага. продукты. В этой статье, на основе традиционного процесса сварки оплавлением паяльной пасты, разработан и представлен новый процесс вторичной сварки оплавлением для улучшения сварочной полости и решения проблем склеивания и растрескивания пластикового уплотнения, вызванных сварочной полостью.
2. Полость для сварки оплавлением и производственный механизм для печати паяльной пасты
2.1 Сварочная полость
После сварки оплавлением изделие было проверено рентгеновским излучением. Было обнаружено, что отверстия в зоне сварки более светлого цвета возникли из-за недостаточного количества припоя в сварочном слое, как показано на рисунке 1.
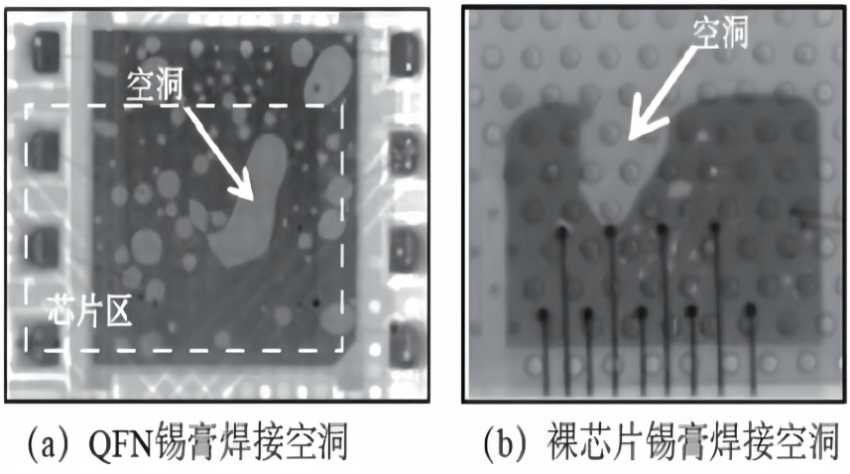
Рентгеновское обнаружение пузырькового отверстия
2.2 Механизм формирования сварочной полости
На примере паяльной пасты sAC305 ее основной состав и функции показаны в Таблице 1. Флюс и оловянные шарики склеены вместе в форме пасты. Массовое соотношение оловянного припоя и флюса составляет около 9:1, а объемное соотношение — около 1:1.
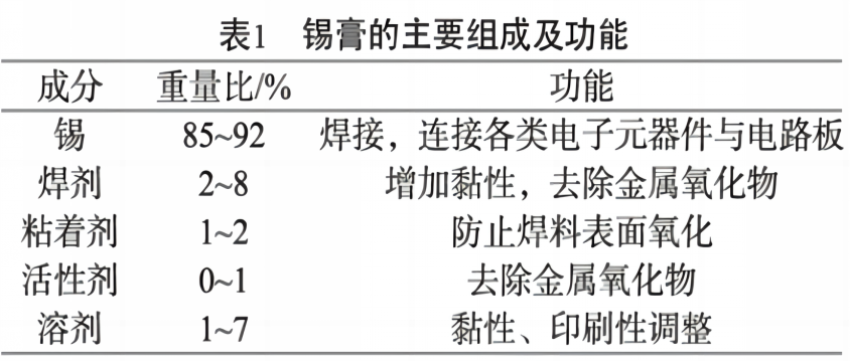
После того, как паяльная паста напечатана и смонтирована с различными электронными компонентами, паяльная паста проходит четыре стадии предварительного нагрева, активации, рециркуляции и охлаждения, когда она проходит через дефлегмовую печь. Состояние паяльной пасты также различается при разных температурах на разных стадиях, как показано на рисунке 2.
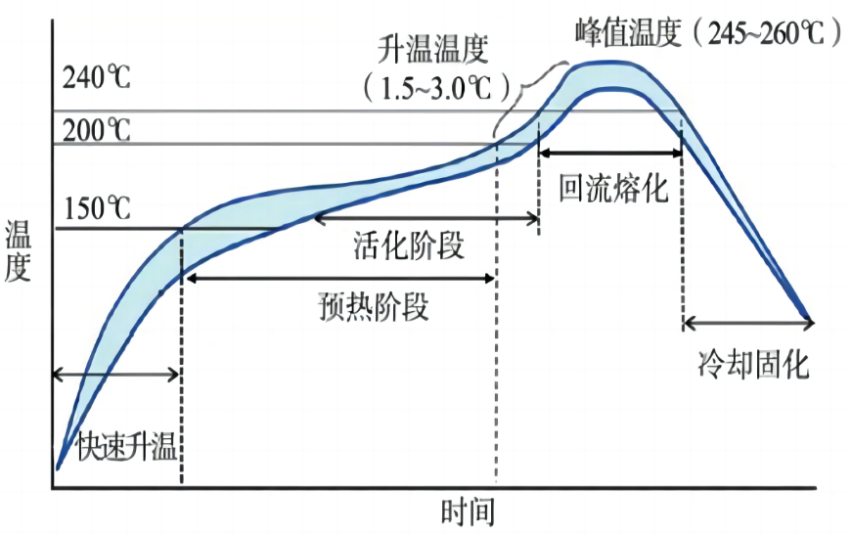
Ссылка на профиль для каждой области пайки оплавлением
На этапе предварительного нагрева и активации летучие компоненты флюса в паяльной пасте при нагревании улетучиваются в газ. В то же время при удалении оксида на поверхности сварочного слоя будут выделяться газы. Часть этих газов улетучивается и покидает паяльную пасту, а шарики припоя плотно конденсируются из-за улетучивания флюса. На стадии рефлюкса оставшийся флюс в паяльной пасте быстро испаряется, оловянные шарики плавятся, небольшое количество летучих газов флюса и большая часть воздуха между оловянными шариками не рассеиваются во времени, а остаток в расплавленное олово и под напряжением расплавленного олова представляют собой сэндвич-структуру гамбургера и захватываются паяльной площадкой печатной платы и электронными компонентами, а газ, завернутый в жидкое олово, трудно выйти только за счет восходящей плавучести. Верхнее время плавления очень короткий. Когда расплавленное олово остывает и превращается в твердое олово, в сварочном слое появляются поры и образуются отверстия для пайки, как показано на рисунке 3.
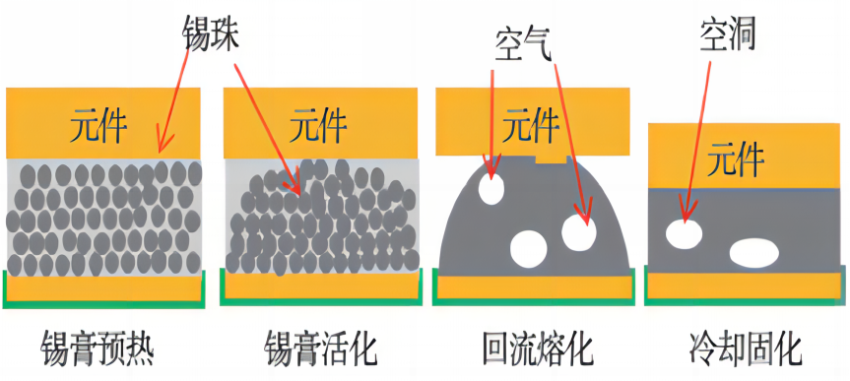
Схематическая диаграмма пустот, образующихся при сварке оплавлением паяльной пасты
Основная причина возникновения сварочной полости заключается в том, что воздух или летучий газ, заключенный в паяльной пасте после плавления, не полностью удаляется. Влияющие факторы включают в себя материал паяльной пасты, форму печати паяльной пасты, количество печати паяльной пасты, температуру рефлюкса, время рефлюкса, размер сварки, структуру и так далее.
3. Проверка факторов, влияющих на отверстия для сварки паяльной пастой при печати оплавлением.
Тесты QFN и голой стружки использовались для подтверждения основных причин образования пустот при сварке оплавлением и поиска способов уменьшения пустот при сварке оплавлением, напечатанных паяльной пастой. Профиль продукта для сварки оплавлением паяльной пасты QFN и голой стружки показан на рисунке 4. Размер сварочной поверхности QFN составляет 4,4 x 4,1 мм, сварочная поверхность представляет собой луженый слой (100% чистое олово); Размер сварного шва голого чипа составляет 3,0 x 2,3 мм, сварочный слой представляет собой напыленный никель-ванадиевый биметаллический слой, а поверхностный слой - ванадий. Сварочная площадка подложки была покрыта никелем-палладием золотом химическим способом, а толщина составляла 0,4 мкм/0,06 мкм/0,04 мкм. Используется паяльная паста SAC305, оборудование для печати паяльной пасты — DEK Horizon APix, оборудование дефлегмовой печи — BTUPyramax150N, а рентгеновское оборудование — DAGExD7500VR.
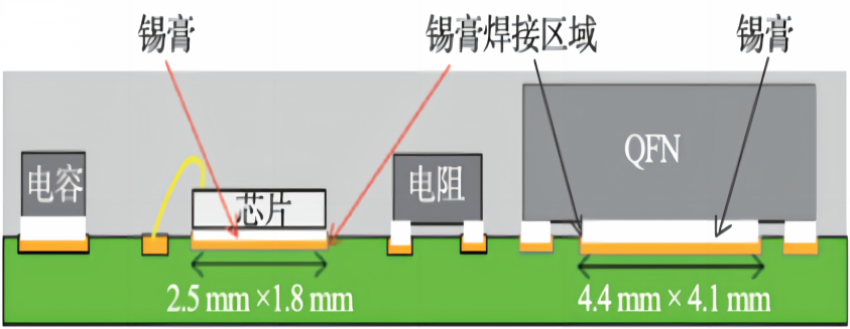
Чертежи QFN и сварки голой стружки
Для облегчения сравнения результатов испытаний сварку оплавлением проводили в условиях таблицы 2.
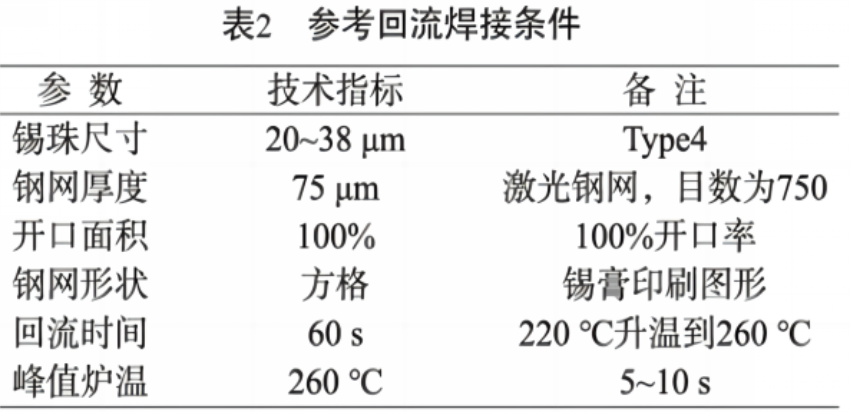
Таблица условий сварки оплавлением
После завершения поверхностного монтажа и сварки оплавлением сварочный слой был обнаружен с помощью рентгена, и было обнаружено, что в сварочном слое в нижней части QFN и голой стружки были большие отверстия, как показано на рисунке 5.
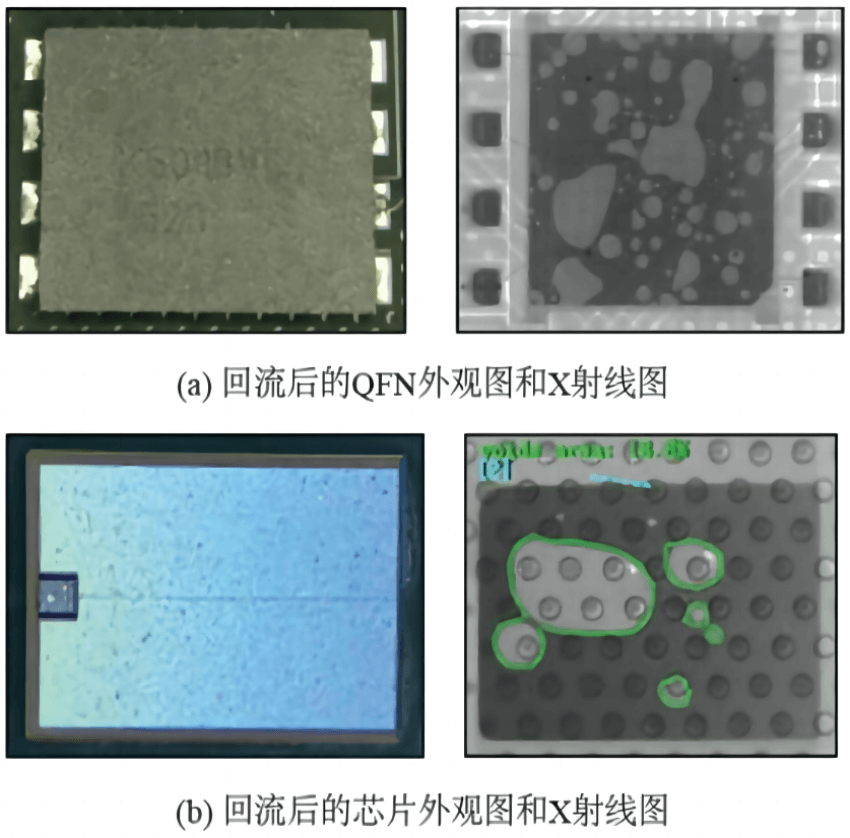
QFN и чип-голограмма (рентгеновская)
Поскольку размер оловянного валика, толщина стальной сетки, площадь отверстия, форма стальной сетки, время орошения и пиковая температура печи - все это влияет на пустоты при сварке оплавлением, существует множество влияющих факторов, которые будут непосредственно проверены испытаниями Министерства энергетики, а также количеством экспериментальных испытаний. группы будут слишком большими. Необходимо быстро отфильтровать и определить основные влияющие факторы посредством теста корреляционного сравнения, а затем дополнительно оптимизировать основные влияющие факторы посредством ДОО.
3.1 Размеры отверстий для пайки и шариков паяльной пасты
При тесте паяльной пасты типа 3 (размер шарика 25–45 мкм) SAC305 остальные условия остаются неизменными. После оплавления отверстия в слое припоя измеряются и сравниваются с паяльной пастой типа 4. Обнаружено, что отверстия в слое припоя существенно не различаются между двумя видами паяльной пасты, что указывает на то, что паяльная паста с разным размером валиков не оказывает очевидного влияния на отверстия в слое припоя, что не является влияющим фактором. как показано на фиг. 6 Как показано.
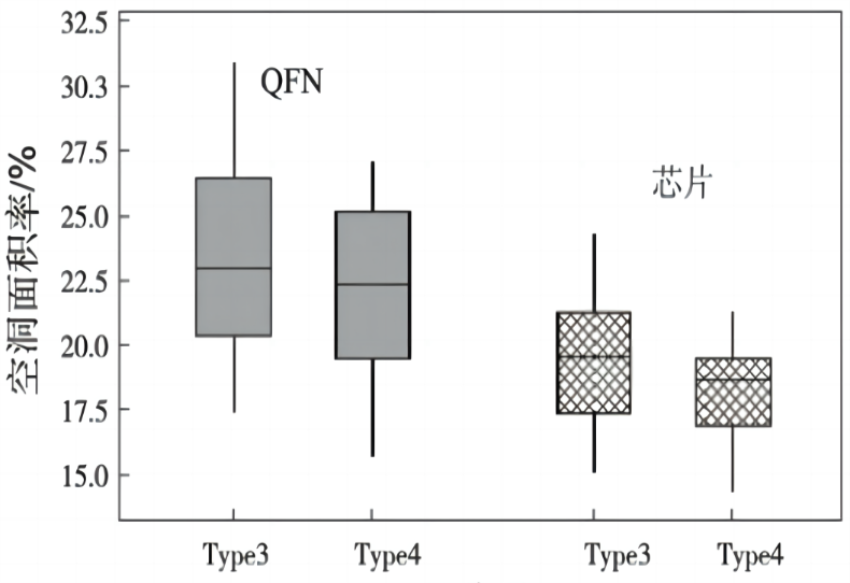
Сравнение отверстий в порошке металлического олова с частицами разного размера
3.2 Толщина сварочной полости и напечатанной стальной сетки
После оплавления площадь полости сварного слоя измеряли с помощью напечатанной стальной сетки толщиной 50 мкм, 100 мкм и 125 мкм, остальные условия оставались неизменными. Было обнаружено, что влияние различной толщины стальной сетки (паяльной пасты) на QFN сравнивалось с влиянием напечатанной стальной сетки толщиной 75 мкм. По мере увеличения толщины стальной сетки площадь полости постепенно медленно уменьшается. После достижения определенной толщины (100 мкм) площадь полости изменится и начнет увеличиваться с увеличением толщины стальной сетки, как показано на рисунке 7.
Это показывает, что при увеличении количества паяльной пасты жидкое олово с орошением покрывается сколом, а выход для выхода остаточного воздуха сужается только с четырех сторон. При изменении количества паяльной пасты выход остаточного воздуха также увеличивается, и мгновенный выброс воздуха, окутанного жидким оловом, или летучего газа, выходящего из жидкого олова, приведет к разбрызгиванию жидкого олова вокруг QFN и чипа.
Испытание показало, что с увеличением толщины стальной сетки лопание пузырьков, вызванное выходом воздуха или летучих газов, также будет увеличиваться, и вероятность разбрызгивания олова вокруг QFN и стружки также соответственно увеличится.
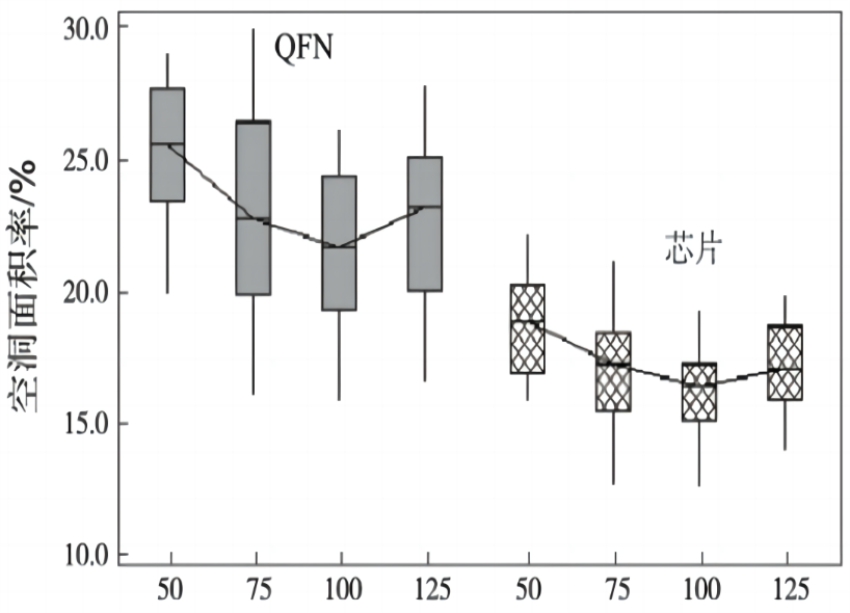
Сравнение отверстий в стальной сетке разной толщины
3.3 Соотношение площадей сварочной полости и отверстия стальной сетки
Была испытана напечатанная стальная сетка со степенью раскрытия 100%, 90% и 80%, остальные условия остались неизменными. После оплавления площадь полости сварного слоя измеряли и сравнивали с напечатанной стальной сеткой со 100% степенью раскрытия. Установлено, что существенной разницы в полости наплавленного слоя в условиях раскрытия 100 % и 90 % 80 % нет, как показано на рисунке 8.
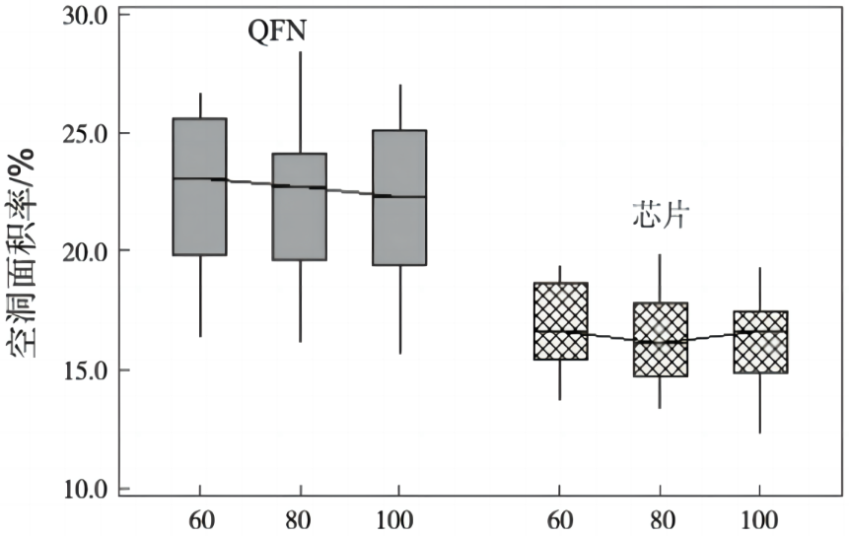
Сравнение полостей различной площади отверстия различной стальной сетки
3.4 Сварная полость и форма напечатанной стальной сетки
При испытании формы печати паяльной пасты полосы b и наклонной сетки c остальные условия остаются неизменными. После оплавления площадь полости сварочного слоя измеряется и сравнивается с печатной формой сетки а. Установлено, что существенной разницы в полости сварочного слоя в условиях сетки, полосы и наклонной сетки нет, как показано на рисунке 9.
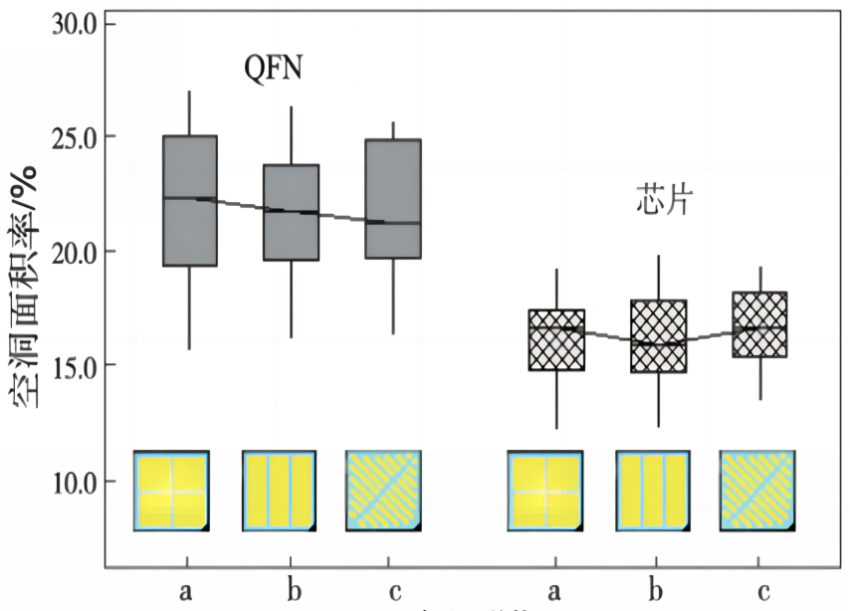
Сравнение отверстий в различных режимах раскрытия стальной сетки
3.5 Сварочная полость и время рециркуляции
После длительного испытания с обратным холодильником (70 с, 80 с, 90 с), остальные условия остались неизменными, отверстие в сварочном слое было измерено после орошения и по сравнению со временем обратки 60 с было обнаружено, что с увеличением время рециркуляции площадь сварочного отверстия уменьшалась, но амплитуда уменьшения постепенно уменьшалась с увеличением времени, как показано на рисунке 10. Это показывает, что в случае недостаточного времени рефлюкса увеличение времени рефлюкса способствует полному перетеканию воздуха, завернутого в расплавленное жидкое олово, но после того, как время рециркуляции увеличится до определенного времени, воздух, завернутый в жидкое олово, будет трудно перелить снова. Время рефлюкса является одним из факторов, влияющих на сварочную полость.
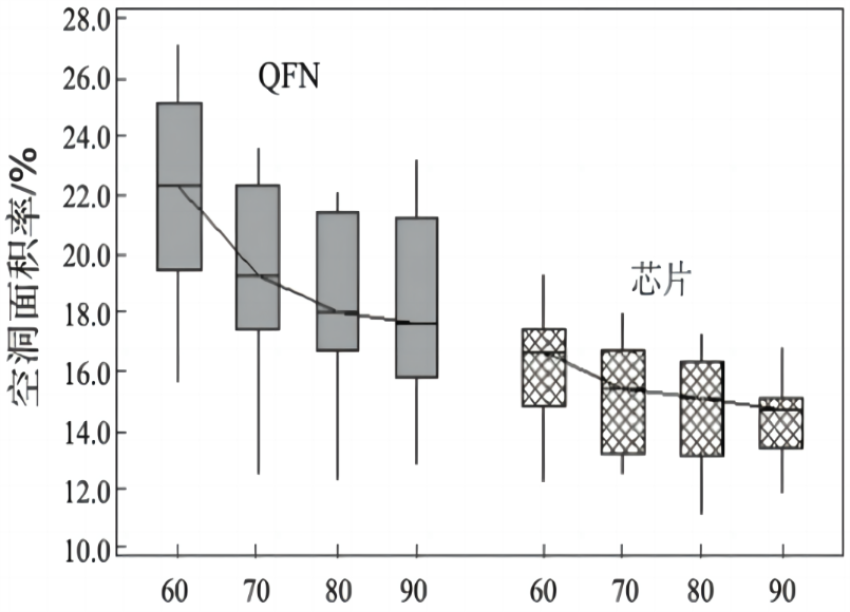
Пустое сравнение разной продолжительности рефлюкса
3.6 Сварочная полость и пиковая температура печи
При испытании на пиковую температуру печи 240 ℃ и 250 ℃ и других условиях без изменений, площадь полости сварного слоя была измерена после оплавления и по сравнению с пиковой температурой печи 260 ℃ было обнаружено, что при различных условиях пиковой температуры печи полость сварной слой QFN и стружка существенно не изменились, как показано на рисунке 11. Это показывает, что различные пиковые температуры печи не оказывают очевидного влияния на QFN и отверстие в сварочном слое чип, который не является влияющим фактором.
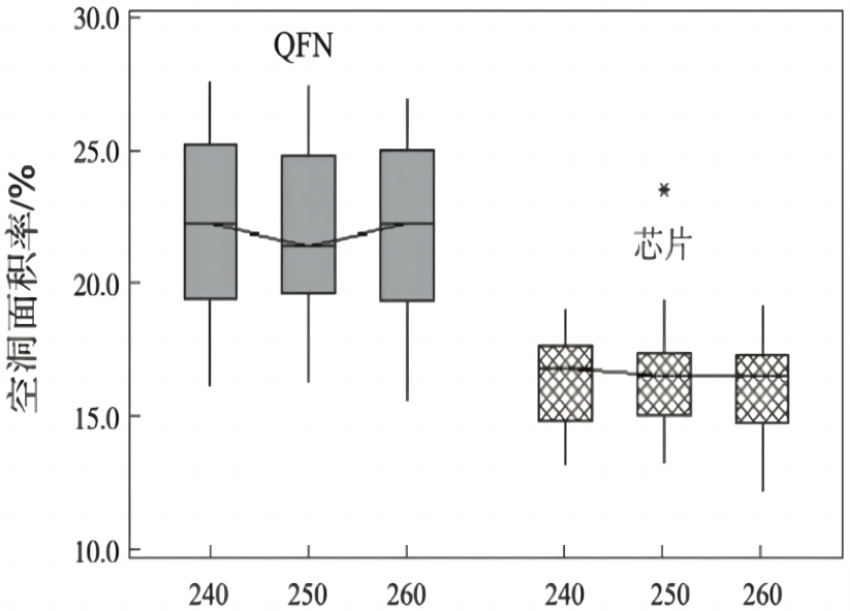
Пустое сравнение различных пиковых температур
Вышеуказанные испытания показывают, что существенными факторами, влияющими на полость сварного слоя QFN и стружку, являются время отлива и толщина стальной сетки.
4 Улучшение сварочной полости для печати паяльной пасты
4.1 Испытание DOE для улучшения сварочной полости
Отверстие в сварочном слое QFN и стружки было усовершенствовано путем нахождения оптимального значения основных влияющих факторов (времени оплавления и толщины стальной сетки). Паяльная паста была SAC305 типа 4, форма стальной сетки была решетчатой (степень открытия 100%), максимальная температура печи составляла 260 ℃, а другие условия испытаний были такими же, как и в испытательном оборудовании. Испытания DOE и результаты показаны в Таблице 3. Влияние толщины стальной сетки и времени оплавки на QFN и отверстия для сварки стружки показано на Рисунке 12. Путем анализа взаимодействия основных влияющих факторов обнаружено, что при использовании стальной сетки толщиной 100 мкм и время рециркуляции 80 с позволяют значительно уменьшить сварочную полость QFN и стружку. Доля сварочных полостей QFN снижается с максимальных 27,8% до 16,1%, а доля стружки в сварочной полости снижается с максимальных 20,5% до 14,5%.
В ходе испытания было произведено 1000 изделий в оптимальных условиях (толщина стальной сетки 100 мкм, время рециркуляции 80 с), а производительность сварочной полости 100 QFN и количество стружки измерялись случайным образом. Средняя доля сварочных полостей QFN составляла 16,4%, а средняя степень образования стружки в сварочных полостьх составляла 14,7%. Очевидно, что степень сварных полостей стружки и стружки снижается.
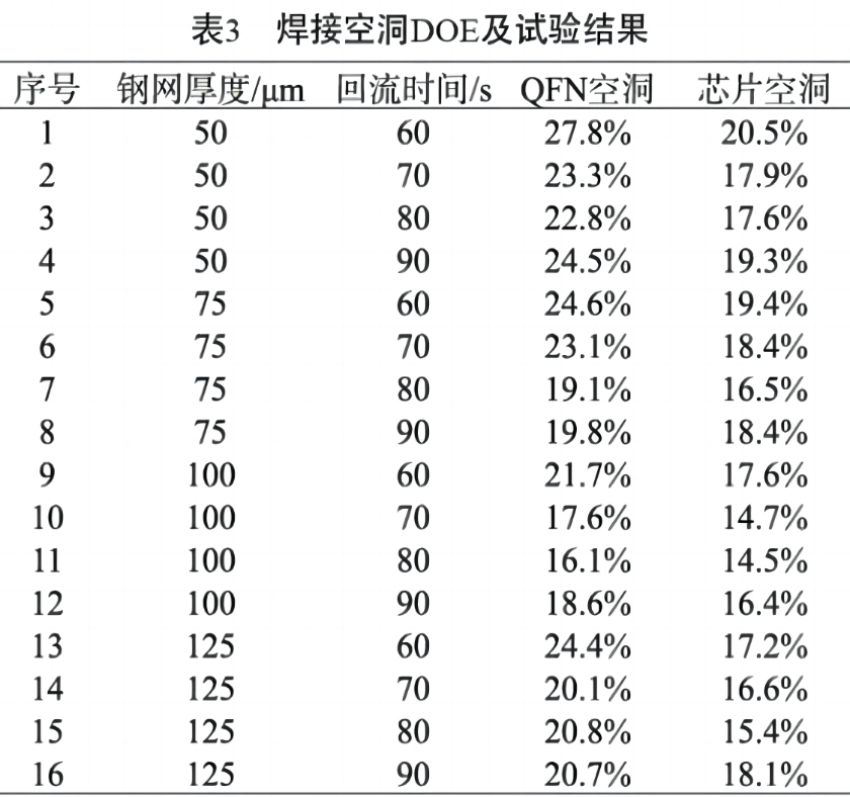
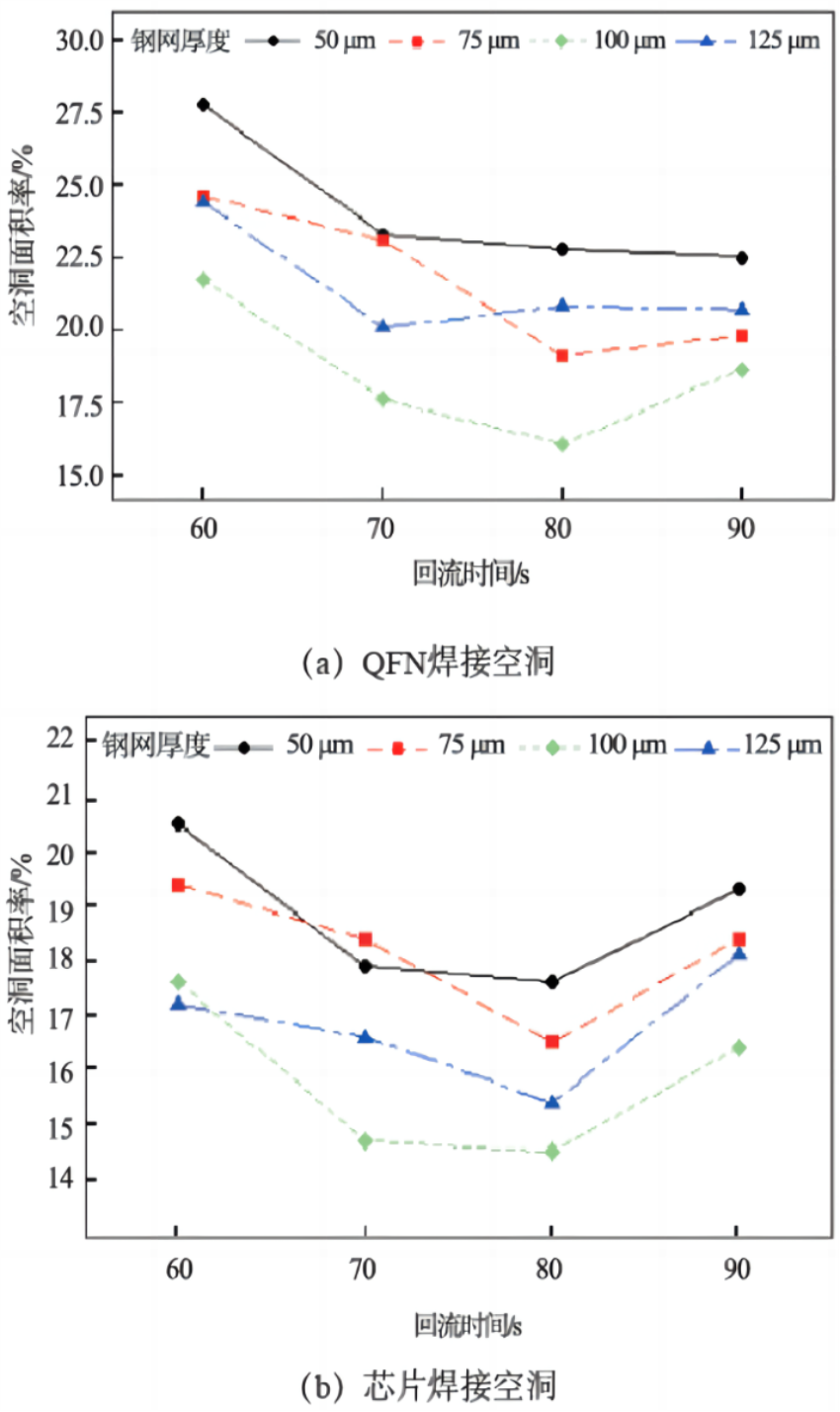
4.2 Новый процесс улучшает сварочную полость
Реальная производственная ситуация и испытания показывают, что, когда площадь сварочной полости в нижней части чипа составляет менее 10%, проблема растрескивания положения полости чипа не возникает во время свинцового соединения и формования. Параметры процесса, оптимизированные Министерством энергетики, не могут удовлетворить требования анализа и устранения отверстий при обычной сварке оплавлением паяльной пасты, и площадь сварочной полости чипа необходимо дополнительно уменьшить.
Поскольку чип, покрытый припоем, предотвращает выход газа из припоя, количество отверстий в нижней части чипа дополнительно снижается за счет устранения или уменьшения газа, покрытого припоем. Внедрен новый процесс сварки оплавлением с двумя отпечатками паяльной пасты: одна печать паяльной пастой, одна печать оплавлением без покрытия QFN и голый чип, выделяющий газ в припое; Конкретный процесс вторичной печати паяльной пасты, заплат и вторичного рефлюкса показан на рисунке 13.
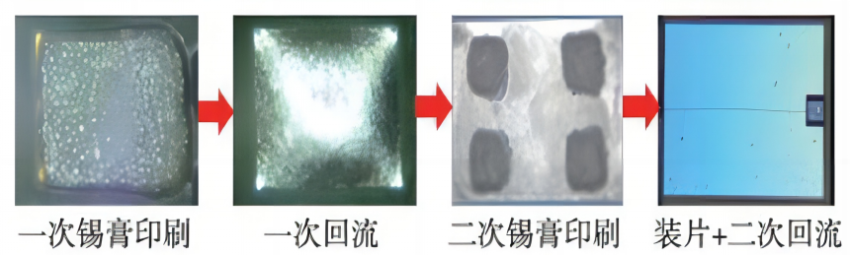
Когда паяльная паста толщиной 75 мкм печатается в первый раз, большая часть газа в припое без покрытия чипа выходит с поверхности, а толщина после рефлюкса составляет около 50 мкм. После завершения первичного орошения на поверхность охлажденного затвердевшего припоя наносятся небольшие квадратики (с целью уменьшения количества паяльной пасты, уменьшения количества утечки газа, уменьшения или устранения брызг припоя), а паяльная паста с толщина 50 мкм (результаты приведенных выше испытаний показывают, что 100 мкм является лучшим, поэтому толщина вторичной печати составляет 100 мкм. 50 мкм = 50 мкм), затем установите чип, а затем вернуться через 80 с. После первой печати и оплавления в припое почти нет отверстий, паяльная паста при второй печати мала, а отверстие для сварки маленькое, как показано на рисунке 14.
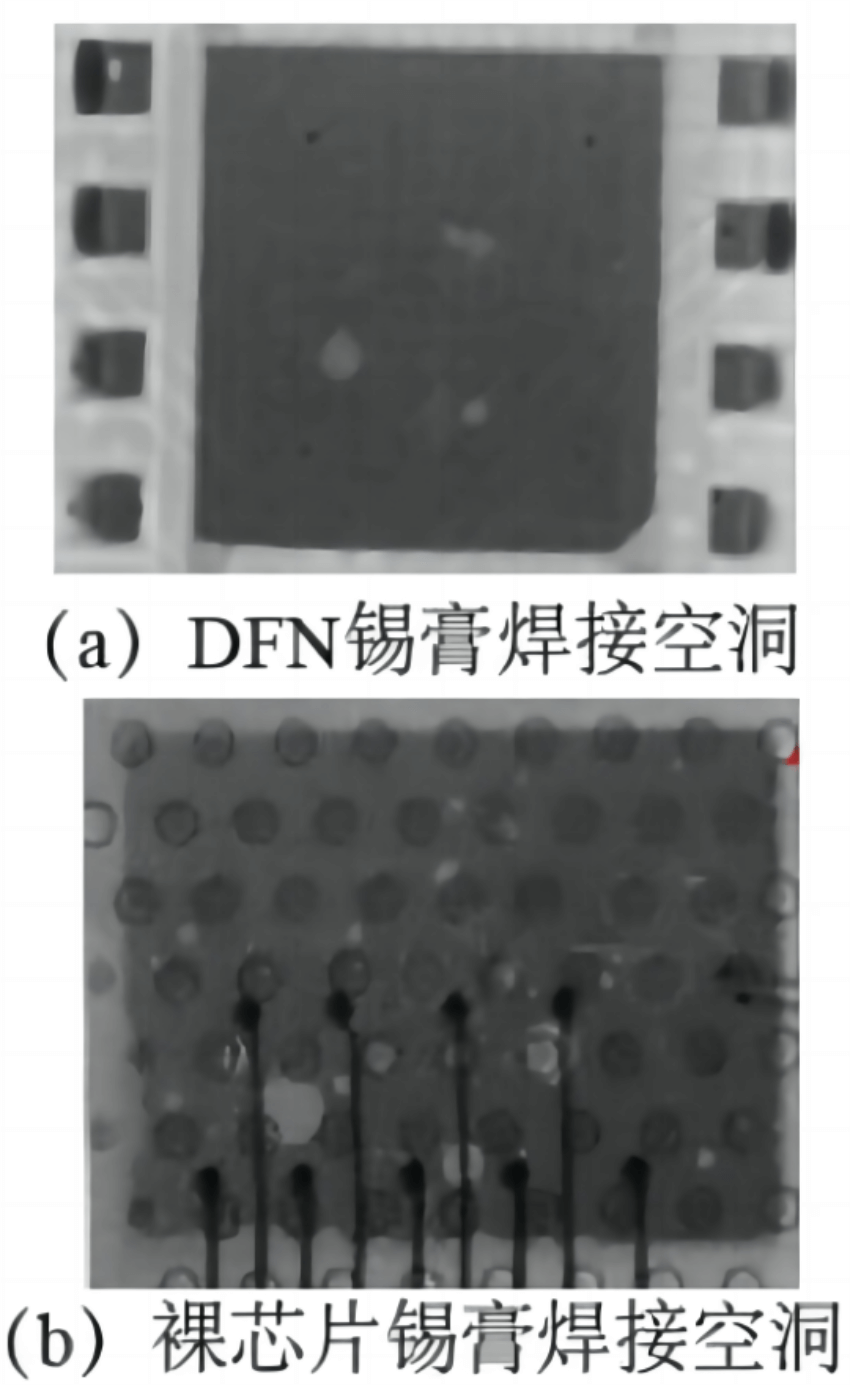
После двух отпечатков паяльной пасты полый рисунок
4.3 Проверка эффекта сварочной полости
Производство 2000 изделий (толщина первой печатной стальной сетки составляет 75 мкм, толщина второй печатной стальной сетки составляет 50 мкм), остальные условия не изменились, случайное измерение 500 QFN и скорость полости для сварки стружки, обнаружило, что новый процесс после первого рефлюкса нет полости, после второго рефлюкса QFN Максимальная скорость сварочной полости составляет 4,8%, а максимальная скорость сварочной полости стружки составляет 4,1%. По сравнению с исходным процессом сварки с однослойной печатью и процессом, оптимизированным Министерством энергетики, сварочная полость значительно уменьшена, как показано на рисунке 15. После функциональных испытаний всех продуктов не было обнаружено сколов.
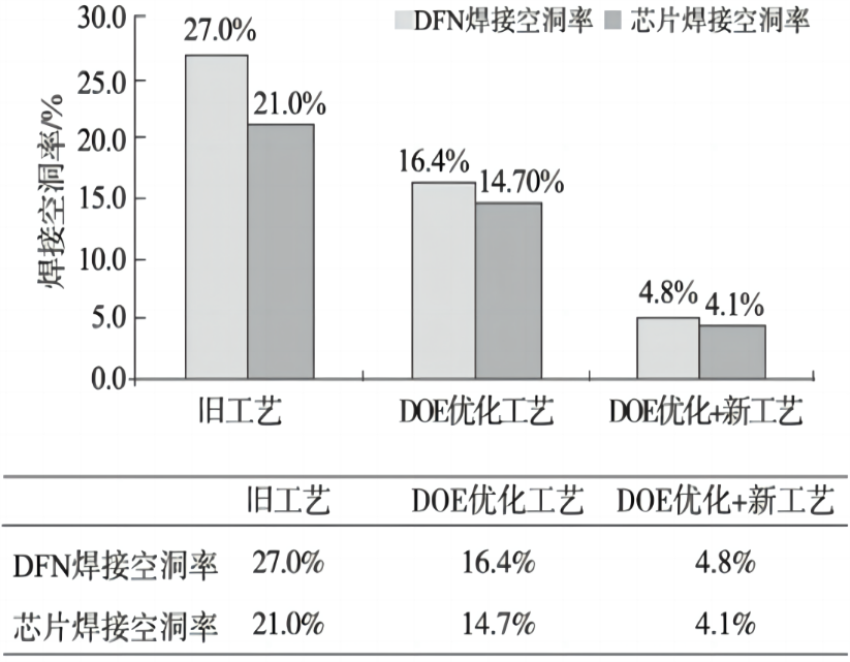
5 Резюме
Оптимизация количества печати паяльной пасты и времени рециркуляции может уменьшить площадь сварочной полости, но производительность сварочной полости по-прежнему велика. Использование двух методов сварки оплавлением с печатью паяльной пасты может эффективно и максимально увеличить производительность сварочной полости. Площадь сварки голого чипа схемы QFN может составлять 4,4 x 4,1 мм и 3,0 x 2,3 мм соответственно при массовом производстве. Скорость сварки оплавлением в полости контролируется ниже 5%, что повышает качество и надежность сварки оплавлением. Исследование, проведенное в этой статье, дает важную информацию для решения проблемы сварочной полости на сварной поверхности большой площади.